Key Attributes
Materials
Copper & Nickel are favored for electroforming due to their stable conductivity and consistent plating, yielding finely detailed product branding and functional components.
Dimensions
Electroforming is most suitable for crafting small, thin product branding elements and functional components—like delicate company logos or intricate emblems—thanks to its precise layering capabilities. However, the same process can scale up to produce larger pieces, including thicker nameplates, by relying on base molds often made from ABS (plastic) or aluminum.
Thickness
Electroformed components can be produced with thicknesses ranging from just a few microns (e.g., 5–10 µm) to several millimeters—often up to 3–5 mm or more, depending on the specific application and the time allowed for metal deposition.
Accuracy/Precision
Ability to capture remarkably fine details—often down to just a few microns in precision—by controlling variables like current density, solution chemistry, and plating time. This layer-by-layer deposition method allows even the smallest grooves, lettering, and textures to be faithfully replicated.
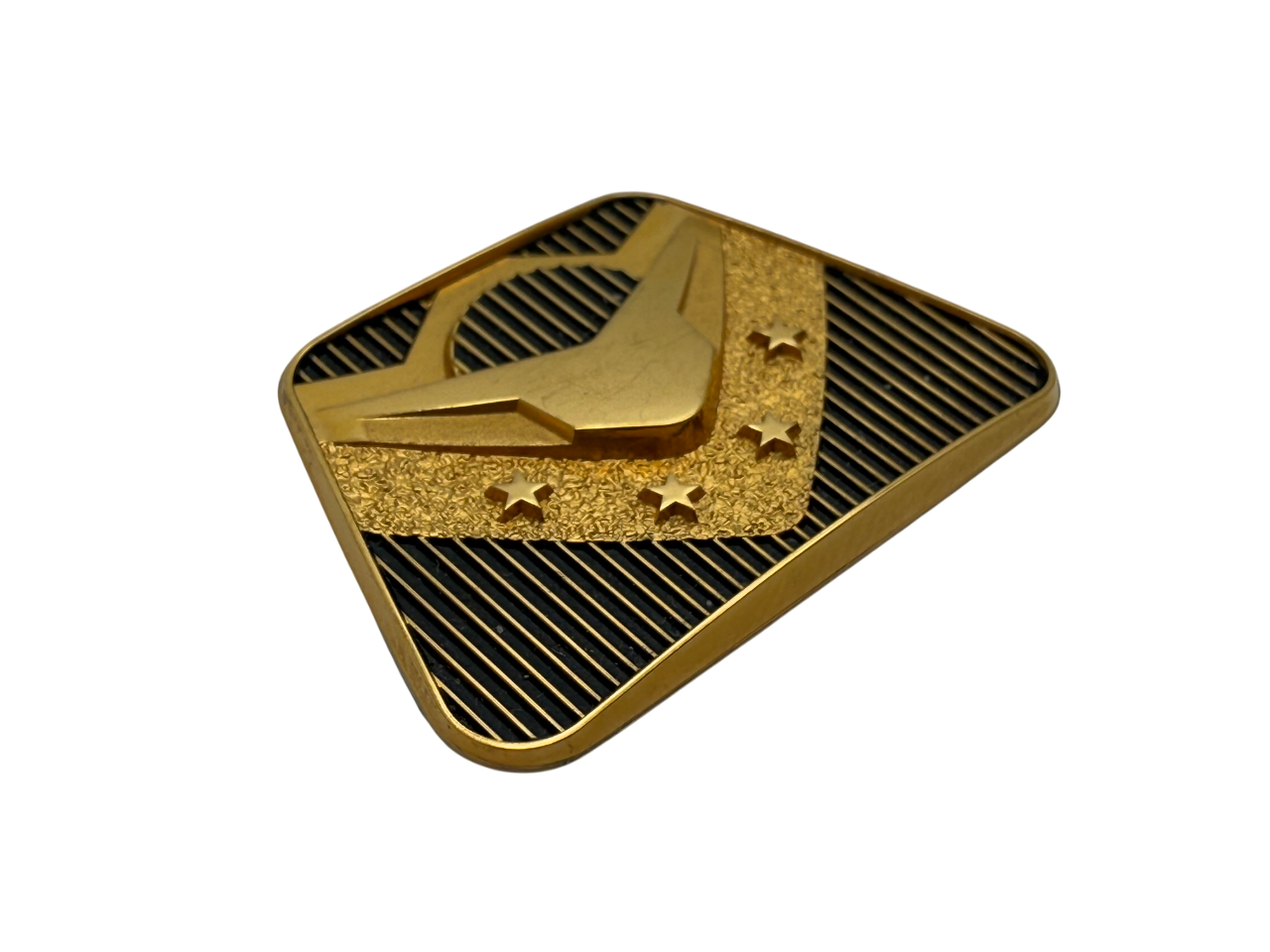
Advantages of electroroming
- Delivers cost-effectiveness for various production volumes.
- Creates crisp, sharply defined edges.
- Produces smooth, stress-free parts free of burrs.
- Easily forms intricate geometries and complex configurations.
- Eliminates the need for costly, rigid tooling.
- Supports three-dimensional growth, enabling additional layers to form in multiple directions.
- Offers outstanding design versatility and fast iterations through advanced photo tooling.
- Scales from initial prototyping to full-scale industrial manufacturing.
- Ensures consistent, repeatable results through meticulous process control and tight tolerances.
- Achieves exceptional accuracy, holding tolerances as tight as ±2 microns.

Create emblematic impressions using electroforming
Imagine your product branding crafted with such precision that every radiant curve and contour seems alive with possibility. Electroforming elevates these designs into tangible metallic details—whether it’s a metal company logo plate on a high-end product, or a decorative flourish on luxury packaging—showcasing a depth and intricacy beyond what traditional methods can achieve. Each luminous facet draws the eye and captivates the senses, forging a memorable emotional bond between your brand and its audience.
Electroform for different industries
-
Automotive
Empowering automotive manufacturers to craft exceptionally detailed emblems, badges, and trim components with minimal stress and tooling costs, all while achieving superior precision and durability.
-
Cosmetic
Enables cosmetic brands to create ultra-thin, precisely detailed labels for different products such as labels for luxury perfume bottles and packaging.
-
Wine & Spirits
Electroformed labels gracefully envelop wine bottles with delicate, intricately detailed designs that shimmer with elegance, transforming each bottle into a captivating symbol of luxury and craftsmanship that enchants every glance.
-
Cleaning
This step is critical to ensure the substrate's surface is impeccably clean, as any residues can interfere with the adhesion and quality of the metal deposition. The substrate, often a metal sheet, undergoes a thorough cleaning and degreasing process to remove all contaminants, oils, and debris, creating an optimal surface for coating.
-
Coating
After cleaning, the substrate is coated with a light-sensitive photoresist or polymer layer. This coating is crucial as it will form the template for the metal structure. The thickness and uniformity of the coating directly impact the resolution and accuracy of the pattern to be formed.
-
Exposing
The coated substrate is then exposed to ultraviolet (UV) light through a mask that contains the desired pattern. This exposure process alters the photoresist's solubility: the areas exposed to UV light become insoluble, while the unexposed areas remain soluble. This step is pivotal for defining the precise and intricate details of the final metal object.
-
Developing
Following exposure, the substrate is developed, washing away the soluble areas of the photoresist and leaving behind a physical representation of the pattern. This stage is where the meticulous details begin to take shape, with the remaining photoresist serving as a mold for the metal deposition.
-
Electrodeposition
During this central phase, the substrate is immersed in an electrolytic bath containing a solution of the desired metal ions. When a direct current is applied, metal ions are attracted to the exposed conductive areas of the substrate, building up the structure layer by layer. The thickness, density, and uniformity of the metal layer can be precisely controlled, allowing for the creation of complex and detailed structures.
-
Harvesting
Once the metal has reached the desired thickness, the electroformed object is carefully separated from the substrate. This step reveals the finished product, which can exhibit extremely fine details and smooth surfaces. If the photoresist was used as a temporary mold, it is removed, often leaving the pure metal structure.
-
Automotive
Learn MoreElectroforming is a versatile and precise technique ideal for the automotive industry, especially for on-product branding purposes. This process allows for the creation of intricate and durable metal badges, logos, and nameplates that can withstand the automotive environment's rigorous demands. Electroforming can produce complex shapes and fine details, offering a level of craftsmanship that enhances the brand identity on various car parts. Automotive manufacturers can utilize this technique to create distinctive and high-quality branding elements that reflect the vehicle's prestige and the manufacturer's attention to detail, elevating the overall perception of the brand.
-
Eyewear
Learn MoreIn the eyewear industry, electroforming offers a unique opportunity for branding, allowing for the creation of high-precision, intricate designs that can significantly elevate the product's aesthetic and brand perception. With electroforming, eyewear brands can achieve crisp, detailed, and durable badges, nameplates, decorative trims, and other branding elements directly on their products. This method is especially beneficial for producing premium, detailed branding components that resonate with consumers seeking quality and sophistication in their eyewear choices. Trailblazer Badges utilizes electroforming to provide a wide range of aesthetic possibilities, including intricate details and custom textures, enhancing the visual appeal of eyewear frames and contributing to a brand's identity
-
Motorcycle
Learn MoreElectroforming can significantly benefit the motorcycle industry, especially for on-product branding purposes. This precision manufacturing process is ideal for creating custom badges that showcase the motorcycle's make, model, and heritage, enhancing its visual identity and appeal. By utilizing electroforming, manufacturers can produce intricate and durable badges that withstand the rigors of the road while maintaining their aesthetic quality. This method allows for the creation of badges with unique textures, finishes, and detailed designs that can reflect the brand's ethos and resonate with riders and enthusiasts alike. Such custom badges can be strategically placed on various parts of the motorcycle, such as the fuel tank or side panels, serving as a powerful branding element that elevates the motorcycle's overall appearance and market positioning.
-
Sporting Goods
Learn MoreElectroforming can significantly enhance the production of sporting goods by creating components that are not only precise but also aesthetically appealing. This process is ideal for producing intricate details and complex shapes, offering you a level of design flexibility that is hard to achieve with other manufacturing methods. When it comes to on-product branding in the sporting goods industry, electroforming stands out for its ability to produce crisp, clean, and durable logos or designs that can endure rigorous use and maintain their appearance over time. This method allows you to create unique, high-quality branding elements that can set your products apart in a competitive market, offering superior durability and precision compared to traditional manufacturing methods. In a sector where branding and product differentiation are key, electroforming provides a cutting-edge solution that can elevate your brand's visibility and appeal to consumers.
-
Electronics
Learn MoreIn the fast-evolving electronics industry, electroforming is a pivotal technology that stands out for its precision and efficiency, particularly in manufacturing components with intricate designs. This method is highly beneficial for creating ultra-fine features, essential for the miniaturization trend in electronics, offering you the capability to produce parts with complex geometries and exceptional surface quality. Electroforming's precision surpasses traditional methods, enabling the production of components with tighter tolerances and smoother finishes, essential for high-performance electronic devices. When it comes to on-product branding, electroforming offers superior detail and durability, ensuring that branding elements remain intact and visible, even under harsh conditions. This process not only enhances the aesthetic appeal of electronic products but also contributes to brand recognition, providing a durable and effective branding solution that other manufacturing methods can't match. Electroforming in electronics goes beyond branding, offering precision in creating mechanical parts vital for the functionality and reliability of electronic devices.
-
Cosmetics
Learn MoreIn the cosmetics industry, where precision and aesthetics are paramount, electroforming presents a unique opportunity to elevate product design and branding. This manufacturing process stands out for its ability to produce components with intricate details and smooth finishes, making it ideal for creating decorative elements, branding logos, or functional parts on cosmetic packaging and accessories. Electroforming's precision exceeds traditional methods like casting or stamping, allowing for the replication of complex designs with high fidelity. This level of detail enhances the perceived value and appeal of cosmetic products, offering brands a distinct advantage in a competitive market. Additionally, the durability and quality of electroformed parts ensure that branding elements remain intact and visually striking over time, reinforcing brand identity and customer loyalty. By opting for electroforming, cosmetic brands can achieve a blend of functionality, beauty, and precision, distinguishing their products with a touch of sophistication and innovation.
-
Appliances
Learn MoreElectroforming offers a unique advantage in the appliances industry, allowing manufacturers to create components with exceptional precision and complexity. This method is not just for aesthetic enhancements such as appliance badges and nameplates but also for functional parts in appliances, where accuracy and durability are crucial. The technique's ability to produce components with tight tolerances and intricate details makes it ideal for appliances that require high precision, such as coffee filters, sugar screens, and other filtration systems. The process's flexibility allows for customization in design and material selection, catering to the specific needs of various appliances, ensuring that each part functions optimally within its system. Moreover, electroforming's efficiency in producing high volumes of parts with consistent quality and its capability for rapid prototyping make it a superior choice for the appliance industry, where innovation and speed to market are key competitive advantages.
-
Transportation
Learn MoreElectroforming is a versatile technique that can significantly benefit the transportation industry, particularly for trucks, buses, trailers, and other vehicles. This advanced manufacturing process allows for the creation of durable, precise, and intricately designed metal parts, ideal for vehicle badges, emblems, nameplates, and decorative trim. Unlike traditional methods, electroforming provides superior detail and finish quality, ensuring that branding elements on transportation vehicles are not only visually striking but also built to last against harsh environmental conditions. The process offers the ability to produce complex shapes and fine details that other methods can't achieve, making it an excellent choice for enhancing brand recognition and adding a touch of sophistication to various transportation vehicles. With electroforming, you can expect branding components that withstand the test of time and maintain their aesthetic appeal, reinforcing your brand's presence on the road.
-
Furniture
Learn MoreElectroforming offers a unique manufacturing solution for the furniture industry, enabling the creation of exquisite, detailed metal components for tables, chairs, couches, and other furniture pieces. This process allows for the production of intricate designs, logos, and decorative elements with a level of precision and detail unattainable through traditional manufacturing methods. By choosing electroforming, you can elevate the branding on your furniture pieces, ensuring that logos and decorative accents are not only beautifully crafted but also durable and resistant to wear. The superior finish and customization options available with electroforming provide furniture designers and manufacturers with a tool to differentiate their products, enhance aesthetic appeal, and reinforce brand identity in a competitive market. This technique's adaptability makes it suitable for a variety of furniture pieces, offering a durable and visually appealing solution to on-product branding and decorative detailing.
-
Engineering Drawings
Learn MoreOur design team is here to support your vision, offering expert assistance in creating precise engineering drawings and artwork. Whether you need guidance in conceptualizing a new design or refining existing artwork for electroforming, our skilled professionals are equipped to provide the necessary expertise, ensuring your ideas are translated seamlessly into the final product. This collaboration ensures that your designs are not only aesthetically pleasing but also optimized for the electroforming process, guaranteeing the best possible outcome for your project.
-
Samples & Prototyping
Learn MorePrototyping is an essential phase in the manufacturing process, allowing for the early detection of design flaws, refinement of product functionality, and validation of the concept before transitioning to mass production. In the world of manufacturing, creating a prototype helps verify the feasibility of a product, allowing for adjustments based on performance, functionality, and user feedback. This step is crucial for identifying and rectifying potential issues, optimizing user experience, and ensuring cost efficiency before scaling up to mass production.
-
Packaging
Learn MoreIf your electroformed item requires custom packaging, we offer tailored solutions to meet your specific needs. Whether you're looking to enhance the presentation, ensure additional protection during shipping, or align with your brand's aesthetic, our custom packaging options are designed to complement your electroformed products perfectly. This service provides an added layer of value and distinction, ensuring that every aspect of your product, from creation to delivery, reflects the quality and attention to detail that your brand stands for.
-
Warehousing
Learn MoreServices extend beyond just crafting fine custom badges, nameplates, labels, and mechanical parts; we also offer secure storage solutions and direct delivery to the end user at the precise moment required. This comprehensive approach ensures not only the safekeeping of your items but also the convenience of a timely and professional delivery, aligning seamlessly with your schedule and demands. Embrace the peace of mind and efficiency that comes with our all-encompassing service, designed to cater to your specific needs with the utmost professionalism and attention to detail.