
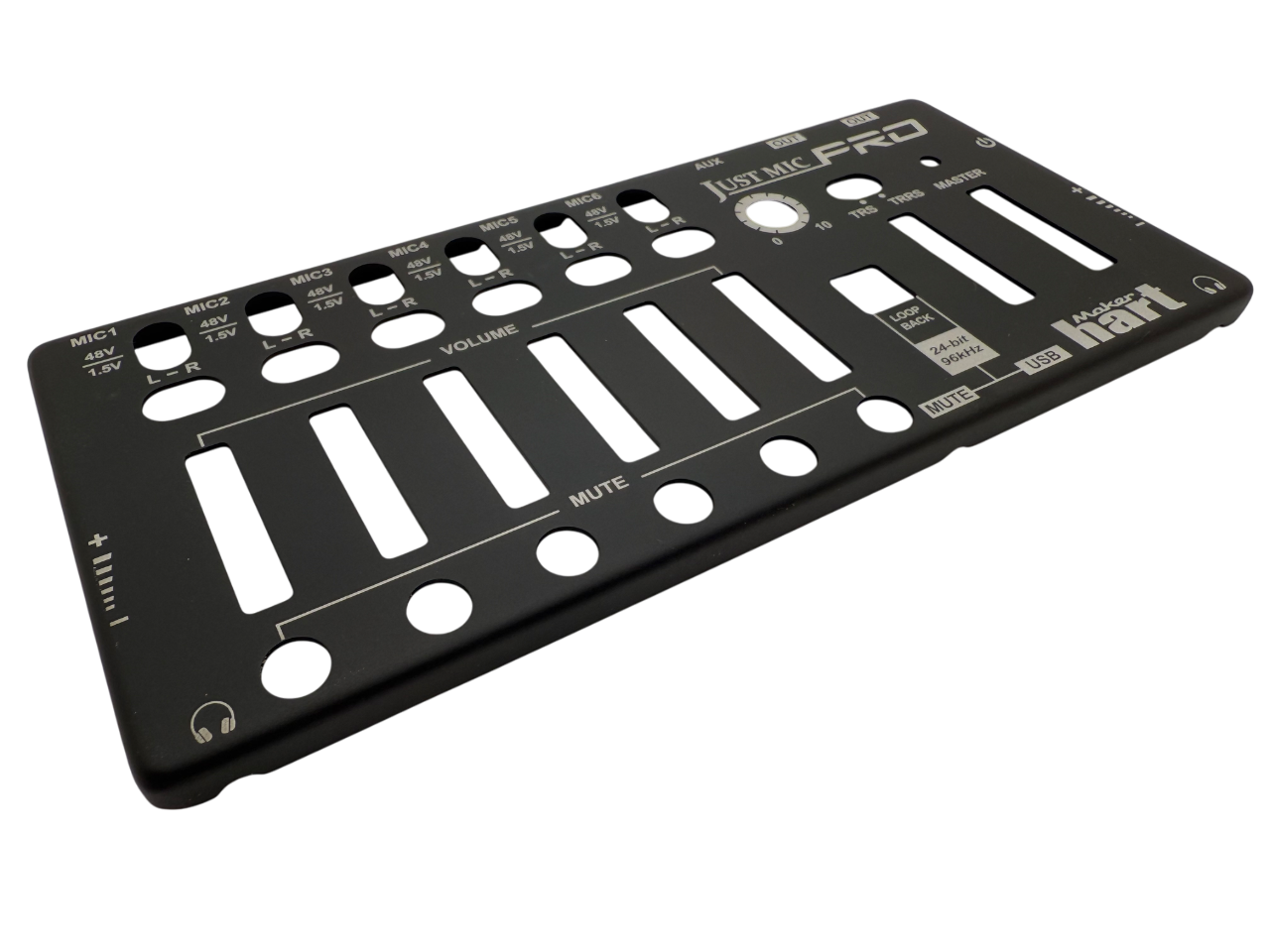
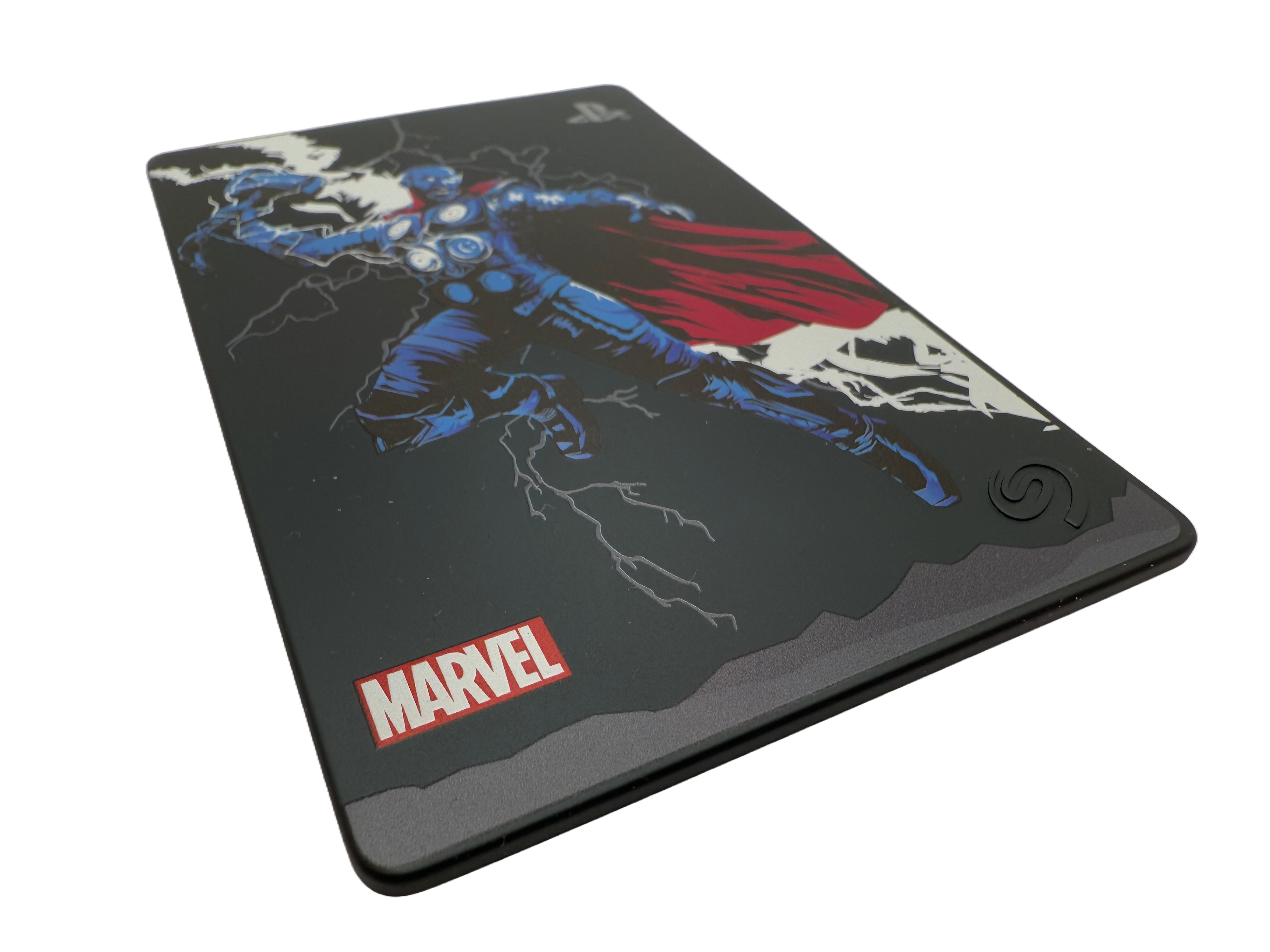

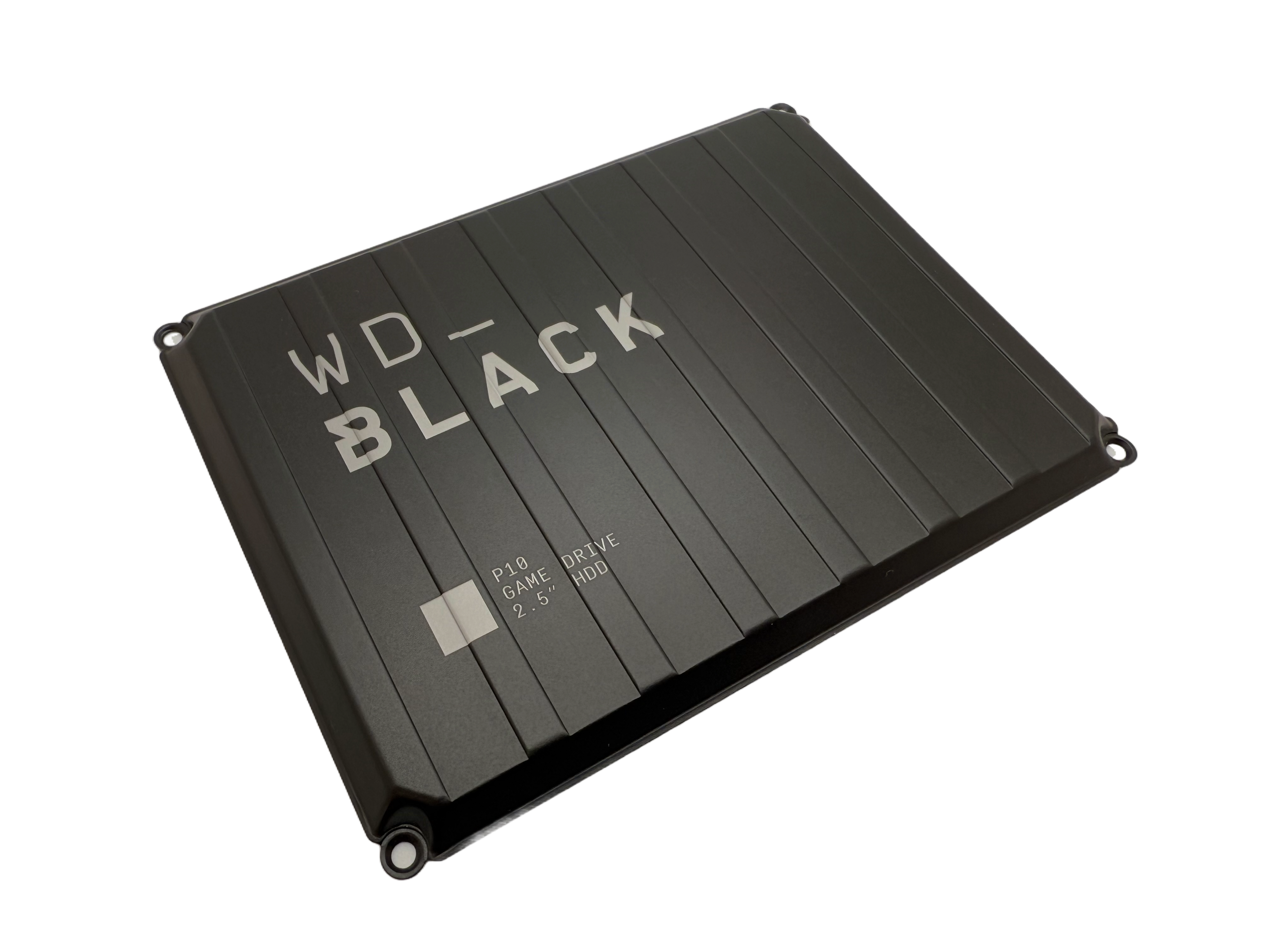
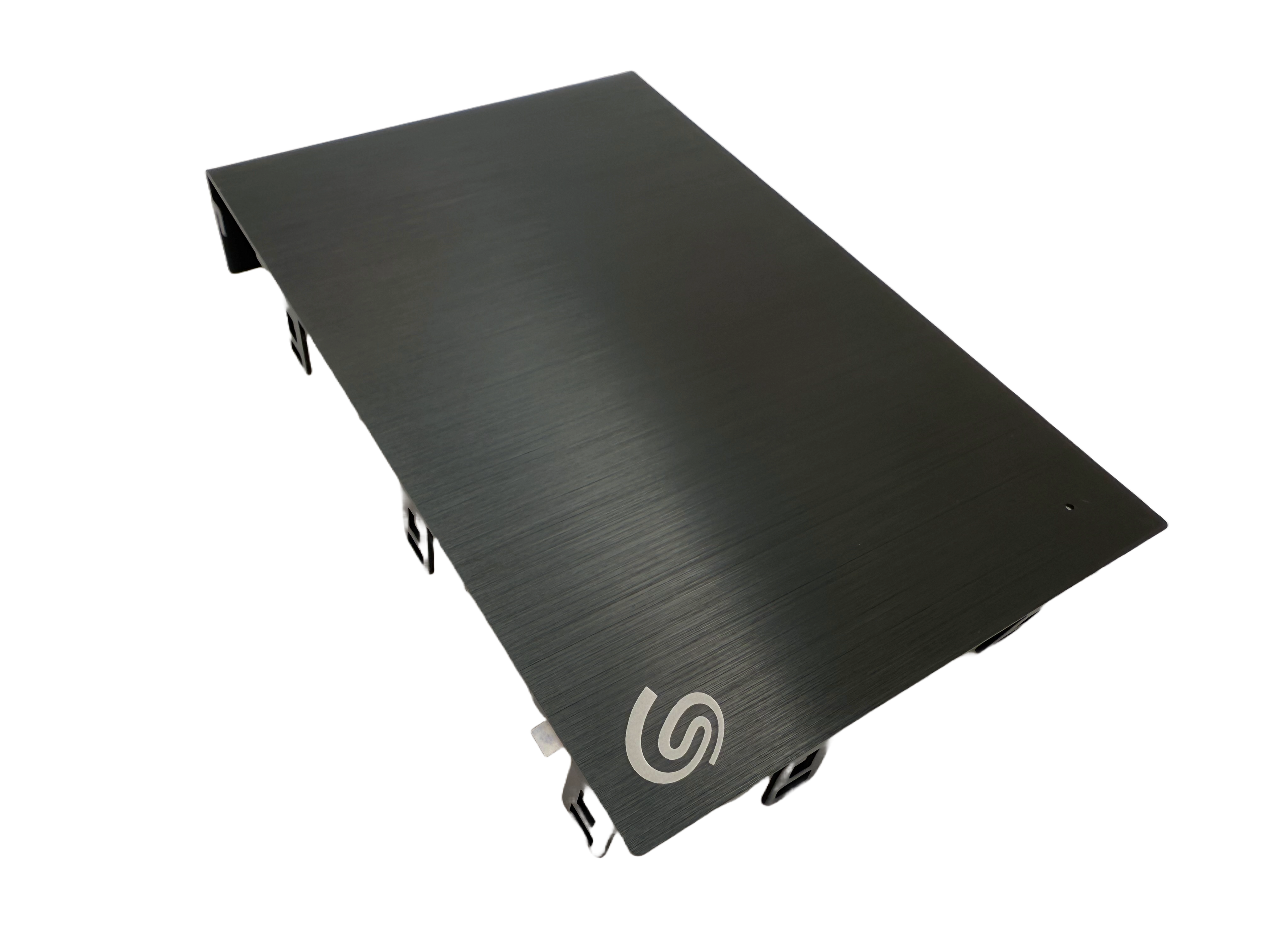
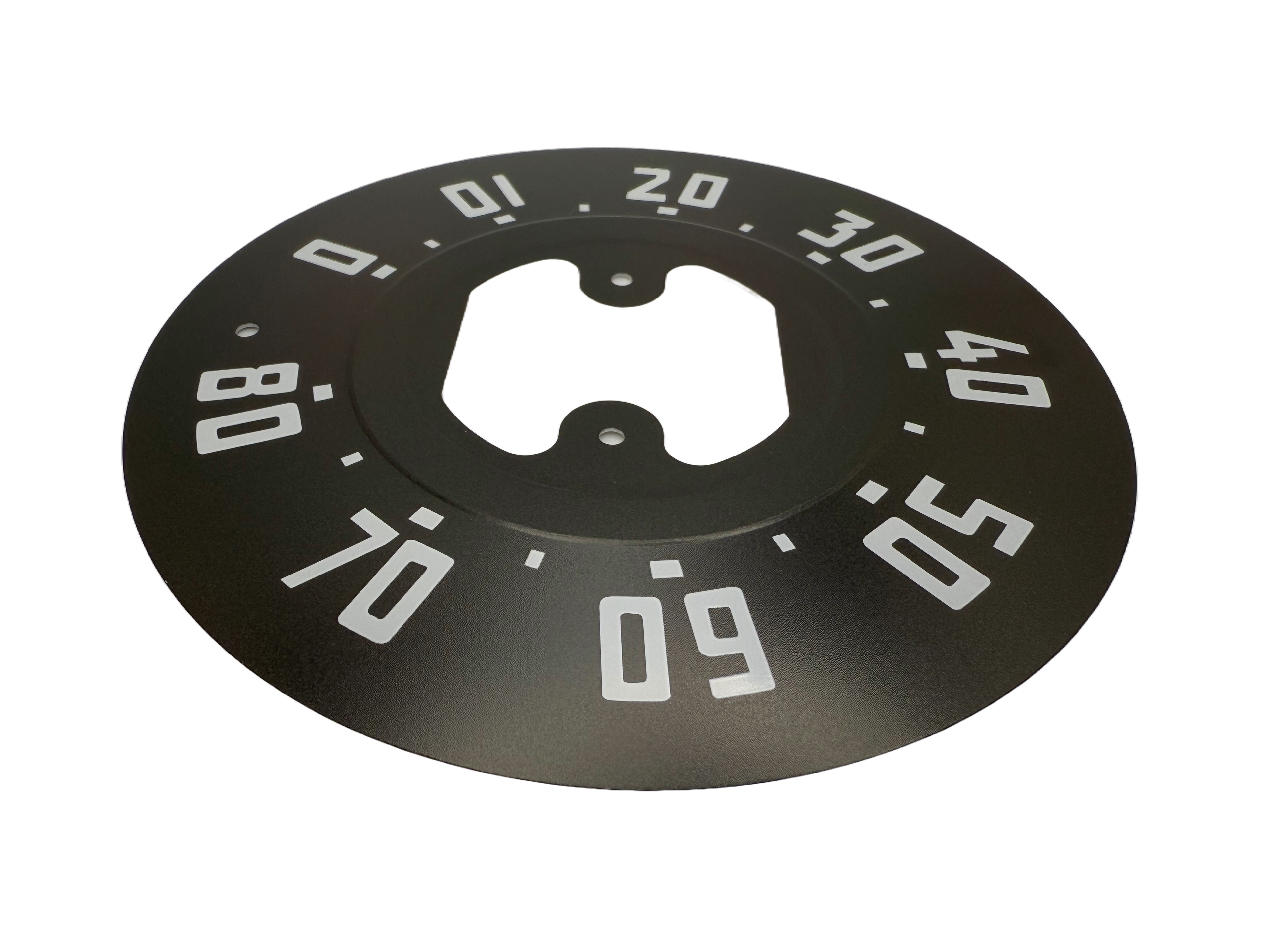
Product Details
Materials
Materials that can be utilized for faceplates include:
- Aluminum
- Anodized Aluminum
- Stainless Steel
Manufacturing Process
We utilize the following techniques to fabricate metal logo plates with precision:
- Metal Stamping/Embossing
- Metal Forging
- Bending
- CNC Milling
Surface Processes
- Commonly utilized surface processes include:
- Anodizing
- Painting - Spray Painting & Injection
- Screen Printing, Digital Printing & Offset Printing
- Engraving
- Hot Stamping
- Gloss
- Brushed
- Matte
- More!
For decorative plates:
- Diamond Cutting
- Enameling
- Physical Vapor Deposition (PVD)
- More!
Attachment
Attachment methods include the following:
- Adhesives
- Mounting Holes - Countersink Holes & Counterbore Holes
- Stud Insertion
- Standoffs
- Tabs
- More!
Artwork/Engineering Drawings
Commonly known as vector or source files. In short, vector files allow us to turn your raised emblem design concepts into tangible products.
If you do not have artwork, don't worry. Our designers can help convert your design into production ready drawings. It is best if you can provide us with pictures, sketches and all other information of your design. We do the rest, free of charge to you.
Designing a badge from scratch does incur a fee and will be dependent on various factors.
No Risk, All Reward Guarantee
How to buy

Unrivalled Resilience With Anodized Faceplates
Anodized aluminum faceplates are engineered to withstand the harshest environments, offering exceptional resistance to corrosion, wear, and chemical exposure. The anodizing process creates a robust aluminum oxide layer that is fully integrated with the base metal, enhancing its hardness and strength. This protective layer acts as a barrier, preventing moisture and corrosive elements from reaching the aluminum, ensuring a longer lifespan for products made from anodized aluminum. This durability ensures that your faceplates maintain their integrity and appearance, even in demanding conditions, providing a reliable and long-lasting solution for your equipment needs.
Join Industrial Titans Who Rely On Trailblazer

Decorative Faceplates Lend An Iconic Finishing Touch
Decorative faceplates can significantly enhance the visual appeal of products such as video game consoles, speakers, amplifiers, appliances and more. By incorporating unique finishes, textures, colors, patterns and more you can turn your products into pieces that captivate consumers. For instance, a sleek, anodized aluminum faceplate with a hairline finish on a high-end amplifier not only exudes sophistication but also complements modern home décor. Similarly, a custom-designed plate on a gaming console can reflect the user's personality, making the device a centerpiece in any entertainment setup.
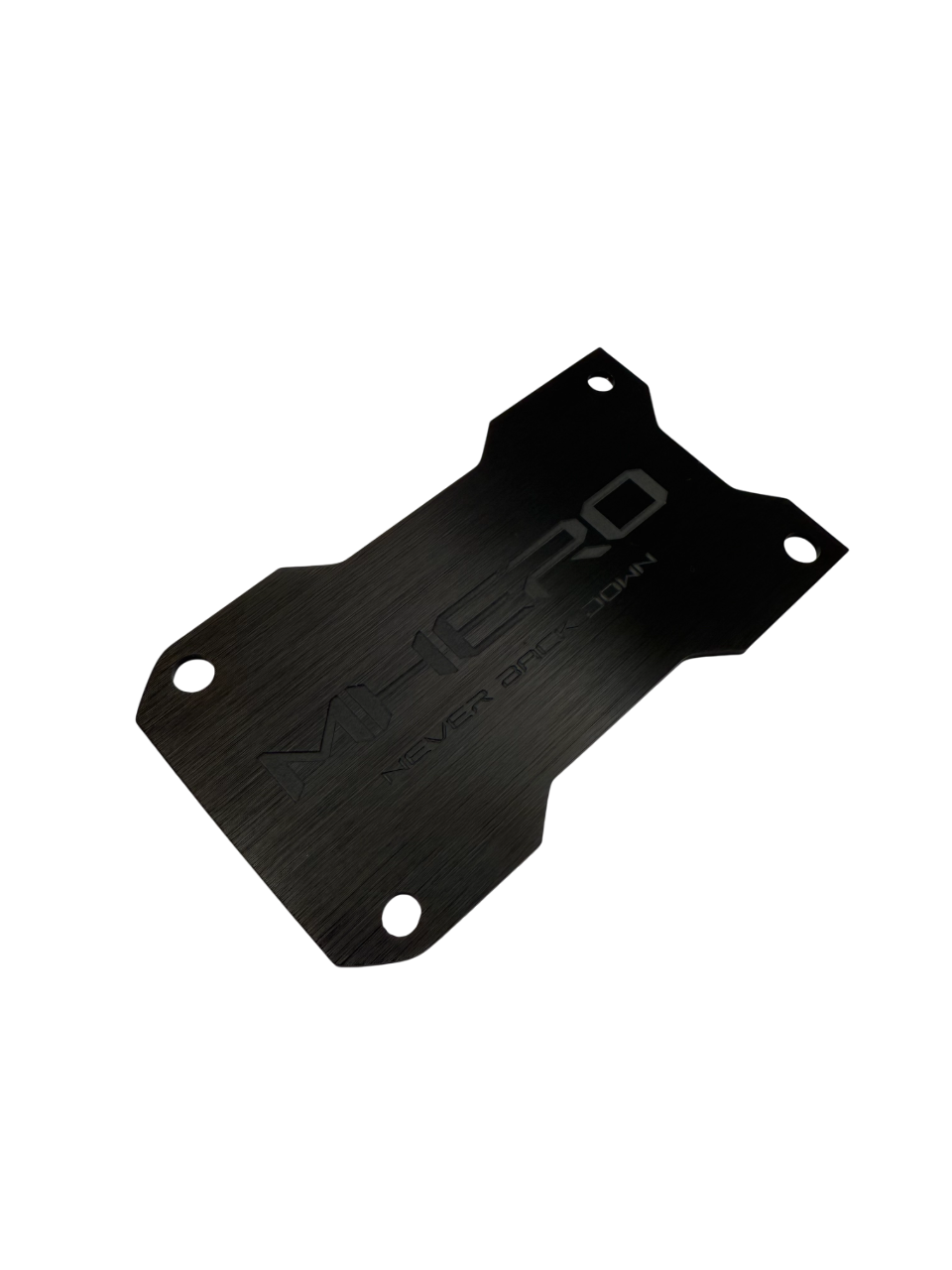
Types of Faceplates & Logos
We offer a diverse selection of fully customizable faceplates, designed to meet your specific requirements and enhance your devices' aesthetics and functionality. Below are some of the options we offer:
- Decorative Faceplates
- Dead Front Panels
- Product Identification
- Instructional
- Safety
- Membrane Switch
- Gauges
- Control Panels
- More!
Innovative Engineering to Help Elevate Within Your Market
-
Electronics
Learn More -
Automotive
Learn More -
Trains & Buses
Learn More -
Industrial
Learn More -
Appliances
Learn More -
Gym Equipment & Fitness Machines
Learn More
Frequently Asked Questions
Are there different specifications different environments?
Yes, each cover plate is designed and fabricated based on multiple factors, which include: chemical exposure, indoor/outdoor exposure, heat, cold, etc.
For example:
- If your plates will be outdoors for extended periods then using anodized aluminum is a must.
- If your plates will be on a video game console, indoors with minimal exposure to extreme temperature changes then aluminum may be the best choice.
What thickness are available?
Most common thickness is between 0.003" to 0.125". However, are able to go thinner or thicker upon request.
What are the most common surface processes?
The surface process will be dependent on the final application. Below are our most commonly used methods:
- Anodizing
- Chemical Etching + Paint Full
- Screen Printing
- Digital Printing
- Engraving
- Reverse Engraving + Paint Fill