Product Details
Materials
The materials we use for boats are carefully selected to be able to withstand rough weather conditions, including saltwater, UV exposure, and constant wear, even the harshest marine environments.
- Aluminum
- Anodized Aluminum
- Stainless Steel
- ABS
- Polycarbonate
- Vinyl
- More!
Manufacturing Process
Wide range of manufacturing processes that are tailored to your specific application and purpose:
- Stamping
- Embossing
- Injection Molding
- Forging
- CNC
- Script - Individual Lettering
- More!
Surface Processes
A large selection of decorative processes to enhance the appearance of your boat's branding:
- Chrome Plating
- Physical Vapor Deposition (PVD)
- Anodizing
- Painting
- Nano-lithography Printing
- Hairline Finish
- Diamond Cutting
- Doming
- Sandblasting
- Hot Stamping
- More!
Sizes & Shapes
We offer an extensive selection of standard shapes and sizes in stainless steel, aluminum, brass, polycarbonate and more. With the capacity to produce script badges/tags in metal or plastic.
Need a unique shape or size? Let us know—we’re here to assist. For a completely custom design, take advantage of our ability to create pre-production samples, allowing you to test the appearance, size, shape and fit before moving to the production stage.
Shipping & Lead Times
Sample Lead Time: 18-21 days from the time we receive artwork approval.
Production Lead Time: 21-28 days from time we receive sample approval. If no sample is required the total lead time is 21-28 days.
Shipping: We ship all orders in the United States free using FedEx Ground or FedEx 2-Day, depending on the size of the package.
We may be able to rush your order if necessary. Please let us know if your order needs expedited shipping.
Minimum Order Quantity
Minimum Order Quantity: 100
Quantity Discounts: 250, 500, 1000, 2500, 5000, 10000+
No Risk, All Reward Guarantee
How To Buy

Built for the Ocean, Designed for Impact
Branding for boats, ships, and yachts is more than just a name; it’s a statement your craftsmanship, values and identity, turning your vessel into a symbol of pride and prestige. Our customizable options include premier metals and plastics, paired with advanced manufacturing processes like injection molding and etching, all designed to craft ship badges that withstand the harsh marine environment. With a large selection of durable finishes that resist corrosion, UV damage, and salt spray, your branding remains as bold and refined as the vessel itself. Let your boat stand out, not just on the water, but as a true reflection of your style and vision.
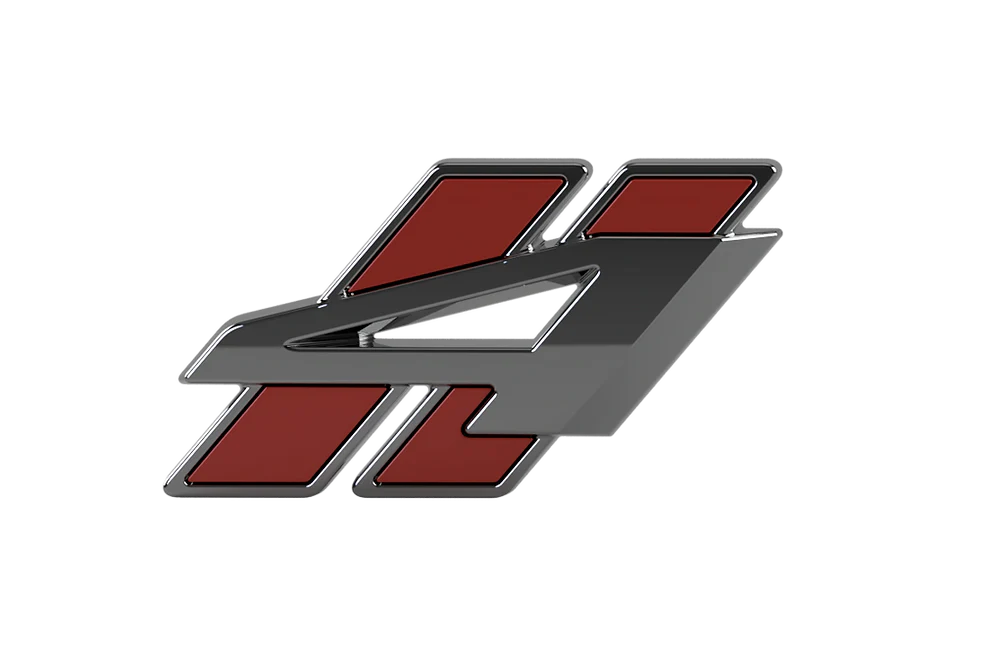
Boat Lettering That Defies The Marine Environment
In the unforgiving marine environment, materials are constantly challenged by factors such as high humidity, salt spray, and UV exposure, all of which can accelerate corrosion and degradation. For instance, relative humidity levels between 80% and 85% can significantly increase corrosion rates. Selecting appropriate materials and protective measures is crucial to prevent structural weakening and to extend the lifespan of your boat logos . By choosing materials designed to withstand these harsh conditions, you ensure the durability and longevity of your marine assets, safeguarding both performance and safety.
Badging That Brands, Protects, and Informs
-
Branding
Ship logos are the signature of your vessel, etched into the transom, gliding along the hull, or standing proudly at the helm. Whether catching the sun on open waters or adding a refined touch inside the cabin, it turns your boat into more than a machine—it becomes the face of your brand.
-
Asset Tracking & Security
Boat tags serve as essential tools for asset tracking and security, embedding serial numbers, barcodes, or RFID technology to monitor and protect vessels. Whether deterring theft, streamlining inventory, or ensuring proper maintenance, they provide a reliable way to safeguard your investment both on and off the water.
-
Compliance & Registration
Product identification is about legitimacy and trust. Registration and compliance nameplates ensure your boat meets industry regulations while displaying key information with durability and precision, giving you the confidence to navigate freely without worry.

Own the Water, Own the Attention: The Art of Yacht Badging
A yacht is more than a vessel—it’s a floating testament to status, craftsmanship, and the pursuit of perfection. The right badge, nameplate, or decorative trim isn’t just an accessory; it’s the finishing touch that transforms steel and fiberglass into an icon of prestige. A gleaming emblem on the hull catches the light as it slices through azure waters, a nameplate on the helm whispers of exclusivity with every touch, and custom trim elevates the yacht’s identity beyond the ordinary. True luxury isn’t just about ownership—it’s about the details that make a statement before a single word is spoken.

Design For Manufacturing Solutions
Where necessary, we can provide you with a comprehensive Design for Manufacturing (DFM) analysis, offering multiple options tailored to your specific requirements. This allows you to choose the most efficient and durable solution for your boat branding that is within your current budget, ensuring you meet both your design vision and functional needs.
- Material Optimization - Right materials are selected for durability, cost-effectiveness, and compatibility.
- Manufacturing Selection - Tailor the design to align with specific manufacturing methods.
- Prototyping and Testing - Designs are reviewed for manufacturability, ensuring that prototypes perform as expected before mass production.
- Cost and Efficiency - Reduce waste and manufacturing inefficiencies by refining designs, helping to meet budget and production timelines while maintaining quality.
Frequently Asked Questions
Are there regulations when developing a boat badge or nameplate?
While decorative badges are generally not regulated, any badges displaying registration numbers or official information must comply with local boating laws.
Are there any size restrictions?
While decorative ship emblems have flexibility in size, those displaying registration information must adhere to specific size requirements as mandated by boating authorities.
How are boat badges attached to the vessel?
Common attachment methods include adhesives, tabs, screws, or rivets, depending on the badge design and boat surface.